Beam welding, a crucial process in the manufacturing landscape, allows for the precise joining of metal components, thereby ensuring structural integrity and longevity. This technique is particularly favored in heavy-duty projects where the demands for strength and durability are paramount. Selecting the right beam welding method involves careful consideration of multiple factors. Failing to account for these factors may result in ineffective welds and compromised structural stability.
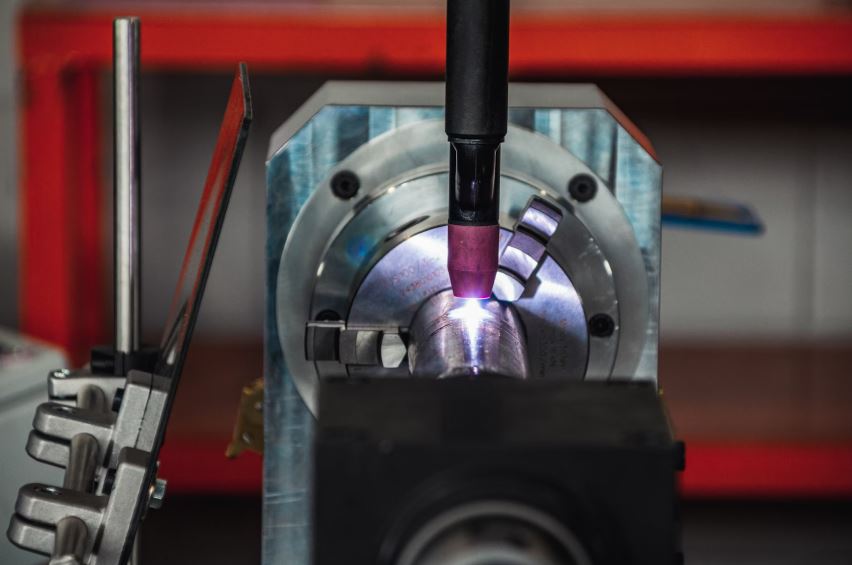
Understanding the Types of Beam Welding
Beam welding is not monolithic; rather, it encompasses several methods, each possessing unique attributes suitable for various applications. Common types include gas tungsten arc welding (GTAW), gas metal arc welding (GMAW), and submerged arc welding (SAW). Understanding these methods is essential when evaluating which best fits a specific project.
GTAW, for instance, offers excellent control over heat input and is often employed for thin-walled components. In contrast, GMAW is known for its speed and versatility, making it a popular choice among industries requiring quick turnarounds. On the other hand, SAW is unparalleled for heavy-duty applications due to its deep penetration and high deposition rates. By assessing these attributes, decision-makers can match their project needs to the appropriate beam welding technique.
Project Specifications and Material Considerations
Every heavy-duty project has unique specifications that dictate the choice of welding technique. For projects involving thicker materials or those that require deep weld penetration, a robust welding method like SAW is often recommended. In contrast, thinner materials may benefit from the precision of GTAW. The type of metal being welded plays a significant role in determining the most suitable welding technique.
Factors such as alloy composition, thickness, and physical properties must be evaluated. Hgh-strength steels might require preheating to minimize stress concentrations, while softer materials such as aluminum may necessitate different approaches altogether. Understanding these material attributes ensures that welders can select the optimal beam welding approach, maximizing efficiency and minimizing errors.
Cost Efficiency and Productivity
Cost considerations are pivotal when selecting a beam welding method for heavy-duty projects. Project managers often grapple with the balance between upfront costs and long-term savings. Techniques that require extensive labor or have high material costs can inflate initial budgets. Methods that produce faster welds or higher-quality outputs can lead to savings on rework and repair costs in the long run.
Implementing a cost-benefit analysis can provide clarity in decision-making. Thus, consulting specialists can be invaluable in approaching this analysis, ensuring an informed decision based on both short-term and long-term projections. While SAW may involve higher initial investments due to equipment and setup, its efficiency and effectiveness in heavy-duty projects can render it cost-effective in the long term.
Welding Environment and Safety Protocols
The environment in which beam welding occurs significantly influences the quality and safety of the process. Conducting welding in uncontrolled environments—such as outdoors or in areas with high wind—can lead to defects. Welding in confined spaces poses additional challenges due to limited ventilation and potential exposure to hazardous fumes. Safety protocols also play a crucial role.
Proper training for operators on equipment handling, as well as having adequate personal protective equipment (PPE), cannot be overstated. Each project should incorporate a risk assessment that accounts for welding processes, materials, and the environment to avoid accidents and ensure compliance with regulations.
Welding Equipment and Technology
Investing in high-quality welding equipment is essential for successful beam welding. The technology employed can directly impact the quality of welds and the efficiency of operations. Advanced welding machines often come with features such as automated controls and enhanced monitoring systems, which help maintain consistent quality and reduce the likelihood of human error. The use of precision-focused technologies, including those implemented by EB Industries in their electron beam and laser welding processes, reflects a broader industry shift toward automation and tighter process control. The evolution of robotic welding systems has captivated the industry, offering customizable solutions for heavy-duty projects while minimizing labor costs. Assessing the latest advancements can position a project for success and streamline operations, yielding a return on investment.
Quality Assurance Processes
Implementing rigorous quality assurance processes is imperative in beam welding. This includes not only initial assessments but also consistent monitoring throughout the welding process. Quality control measures such as non-destructive testing (NDT) can catch flaws before they become critical issues. Best practices in quality assurance additionally extend to proper documentation and traceability.
Ensuring that welds meet the necessary standards and codes is mandatory, particularly in industries like construction and aerospace, where safety is non-negotiable. Promoting a culture of quality within the workforce reinforces the importance of adhering to standards, which can positively influence project outcomes.
Environmental Impacts and Sustainability
Sustainability considerations are increasingly impacting the decision-making process in beam welding. The environmental footprint of welding processes can be significant, particularly regarding emissions and material waste. Evaluating the sustainability of selected techniques is critical for environmentally conscious projects. Investing in energy-efficient equipment and ensuring proper waste management can reduce the overall environmental impact. Sourcing materials that promote recyclability can also be advantageous. Many industries now prioritize sustainable practices, making this a vital factor in strategic decision-making.
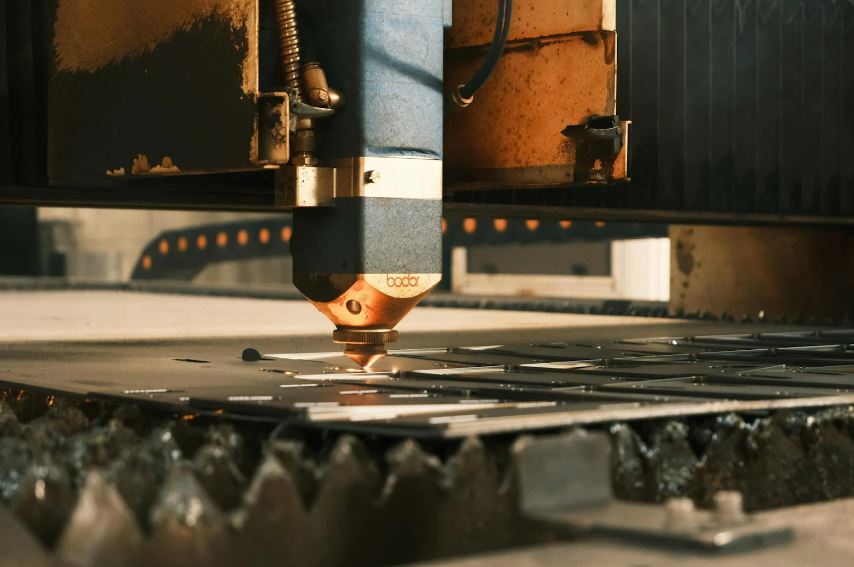
Understanding these factors allows project leaders to make informed decisions about beam welding processes tailored to their specific needs. With precision, quality, and efficiency at the forefront, selecting the right welding technique can dramatically influence the success of heavy-duty projects.